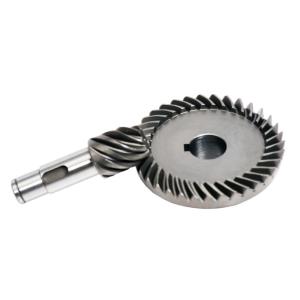
Add to Cart
Products: Pottery reducer gear power transmission machanism with high precision
1. Potttery reducer gear is a gear device used to reduce rotation speed and increase torque in ceramic machinery.
2. The reducer gear is a power transmission mechanism that transmits power through gears of different sizes meshing with each other. It is usually used to reduce the speed and increase the torque. It is an important part of the pottery machine equipment and plays a vital role in the operation of the equipment.
Design of pottery reducer gear:
1. The tooth profile design of pottery reducer gear has strict accuracy requirements, and the processing technology is complex, requiring multiple steps such as gear milling, quenching, grinding, and assembly, so the price is relatively high.
2.In addition, factors such as gear material, accuracy, tooth shape and lubrication method will affect the performance and service life of pottery reducer gears. Therefore, special attention must be paid to the care and maintenance of pottery reducer gears to ensure the normal operation of the equipment.
Potteryg Reducer Gear parameter table:
Products | Pottery reducer gear-power transmission machanism with high precision |
Service | Customized |
Shape | Spiral gear, hypoid gear |
Gear Teeth manufacturing | Milling/Grinding |
Module (M) | ≤4 |
Teeth Accuracy Grade | ISO 6-7 Grade |
Heat Treatment | Carburization and quenching/Carbonitriding/High frequency/Quenched and tempered...... |
Hardness | 54-62HRC |
Application | Construction machinery, ships and mining equipment |
Introduction of the reducer gear :
1. The reducer gear usually consists of a high-speed gear and a low-speed gear. The high-speed gear is connected to the motor output shaft, and the low-speed gear is connected to the working machine shaft. When the motor rotates at high speed, the speed of the output shaft is reduced through the meshing of the gears, and the output torque is increased at the same time to meet the needs of ceramic machinery.
2. The hardness of the reducer gear depends on its material and heat treatment process. Taking the ZDY series hard tooth surface reducer as an example, its gears are usually made of high-quality alloy steel and processed through carburizing, quenching and other processes to make the tooth surface hardness range from HRC54 to HRC62. This high-hardness gear design is designed to improve wear and corrosion resistance, thereby extending the service life of the gear and maintaining high transmission efficiency.
Charactics Grinding Gear:
About our company:
1. we committed to be the best high precision spiral bevel gears supplier. Especially in gear grinding production.
2. Our company was established in 1994. It is a directly affiliated university-run enterprise founded by Central South University Professor Zeng Tao, the leading expert on spiral bevel gears in China.
3. We are a production R&D base specializing in professional design, reserch, manufacture and sales of high-quality small module spiral bevel gears and high reduction hypoid gears and cylindrical gears.
4. Our products can meet industry requiring such as industrial robots, CNC turning and milling compound power cutter tower, industrial sewing machines, reduction gears, bicycles, power tools and aeromodelling.
Our equipments:
Picture display: